Climate Friday | Can Plastic be Fantastic?
26 August 2021
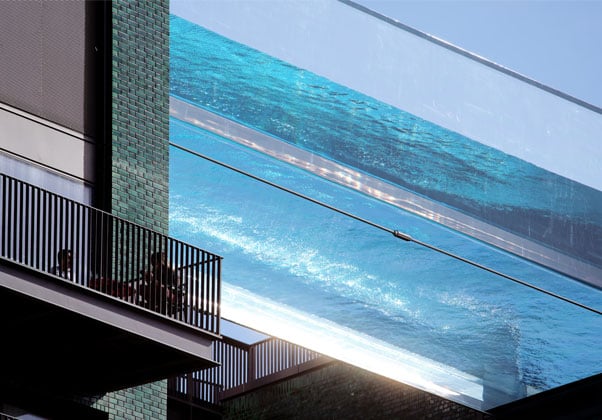
As engineers, we have for decades been selecting materials to best suit the project brief. In the recent past, the criteria have typically been amongst others strength/weight, availability, cost, appearance and speed of construction.
Leading up to EOC signing ‘UK Structural Engineers Declare a Climate and Biodiversity Emergency’ in September 2019 it was clear that this criteria selection had to change.
We have been involved in a huge number of glass projects and been responsible for specifying and selecting a considerable volume. The application of glass for transparent structures is clear. In previous series we have written about glass and, for what is an infinitely recyclable product, the industry needs to do more.
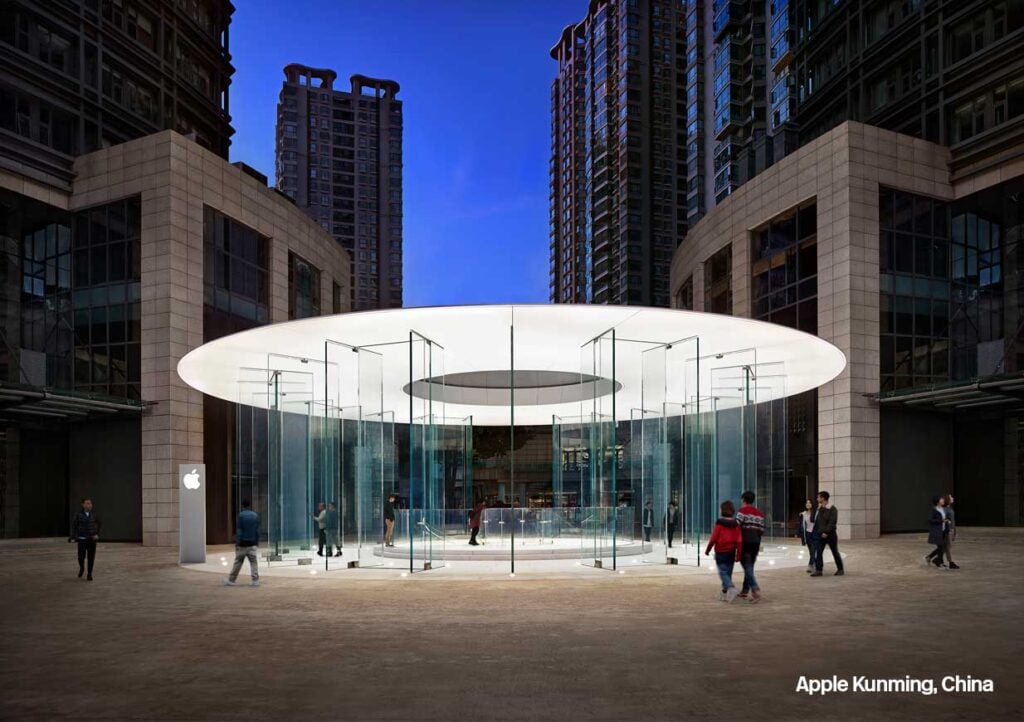
However, we have recently been designing and specifying acrylic as it confers advantageous structural characteristics. For example, acrylic was applied in a roof oculus in Kunming, China and more recently the Sky Pool at Embassy Gardens. Polymers often play a small but very important part in construction but are very rarely the main structural component.
The Sky Pool could not have been achieved in its conceptual or indeed final form in glass; the polymer PMMA (poly methyl methacrylate), commonly known as acrylic, was instead selected. This decision happened some time before ‘Engineers Declare’, and so this event gave us pause for thought to assess our project portfolio.
While acrylic has been recycled for decades it is estimated only 5% is recycled, with the remainder ending in landfill or being burnt for energy. The two established methods of recycling have significant limitations. Mechanical recycling will degrade the resulting recovered material, and Chemical recycling can only take place once.
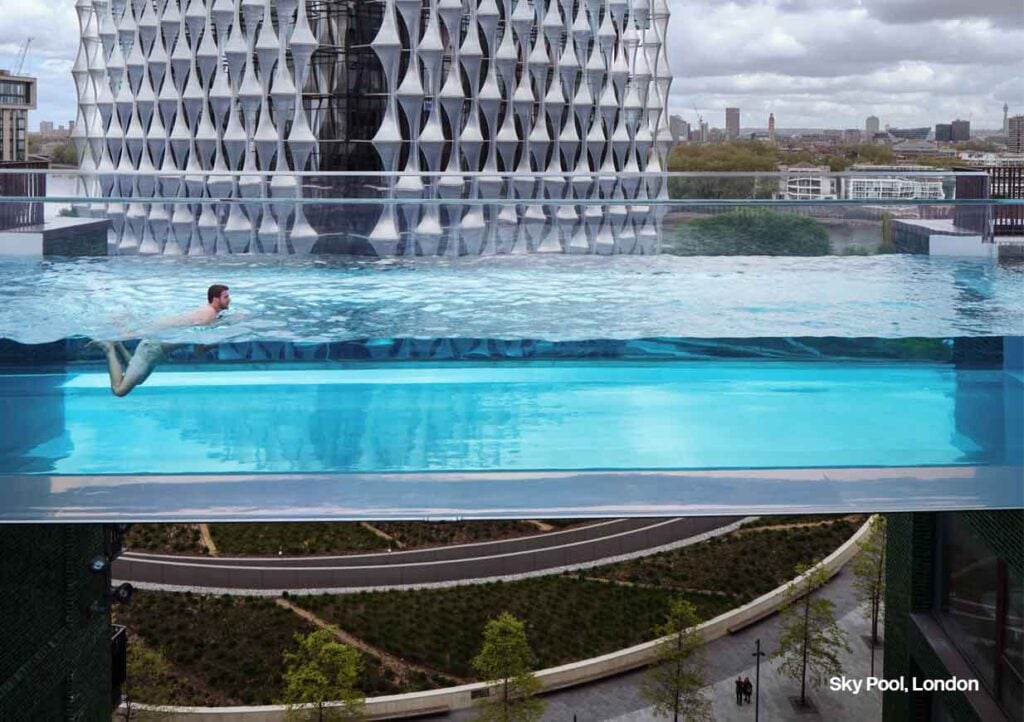
PMMA, like many polymers, is derived from fossil fuels, and once the material has been created it does not break down naturally. So, what were the consequences of using over 50 tonnes in a landmark project? The pool fabricator was using base material from Mitsubishi Chemical Methacrylates, a division of Mitsubishi Chemical and so we investigated this aspect further with them.
Mitsubishi Chemical Methacrylates has been working with Agylix to develop methods of turning acrylic resin (the polymer) into its base construction unit (the monomer). The resulting material is chemically and functionally indistinguishable from a monomer created from raw material.
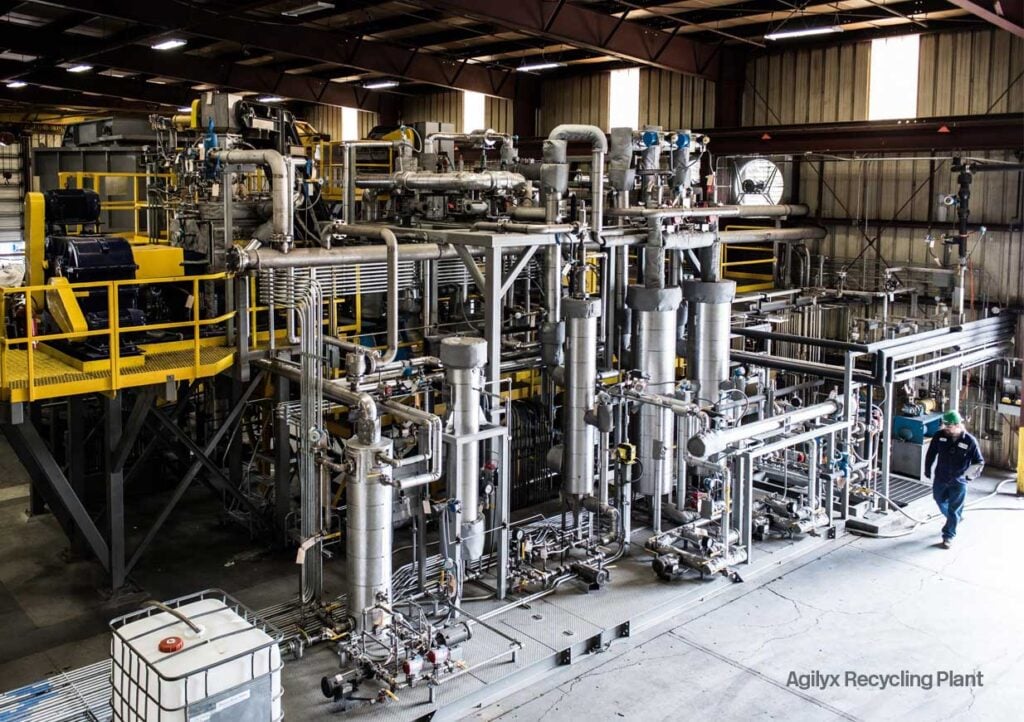
David Smith, Circular Economy Programme Lead at Mitsubishi Chemical describes in greater detail; “Molecular recycling sees acrylic fed into a pyrolysis unit – a high-temperature unit which separates the material into its constituent parts. This produces crude MMA which is then, through a detailed refining process to remove any impurities, turned into recycled MMA of the highest quality.”
Furthermore, the carbon emissions to create the monomer from the waste polymer is reduced by 70% when compared to virgin raw materials.
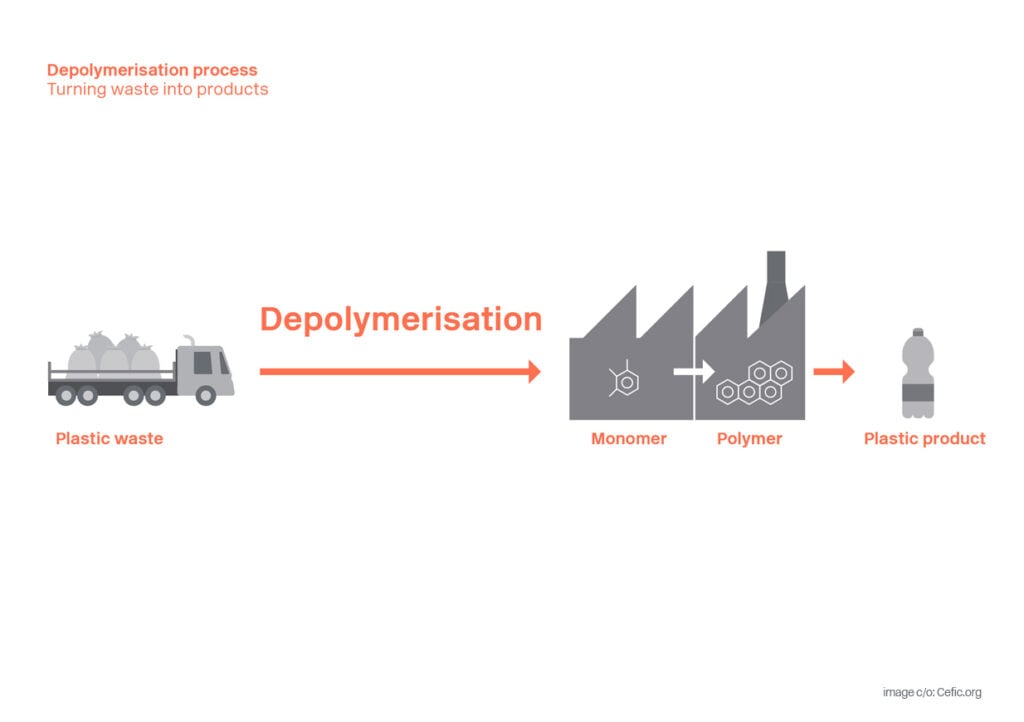
However, as we have discovered in our flat glass research, the capability for material reprocessing must be accompanied by logistics, and this will need to be developed in partnership with the development of the repolymerisation plant – the first of which is due to be open in Europe by 2024.
As we move forward, we must ensure we continue to advance our understanding of the inherent sustainable properties of the materials we use, and how they can be recycled and reused. Of course, these concerns will be balanced alongside the practical realities of a project, so that our clients can make informed decisions on the way to achieving a solution that best serves their needs and the needs of the planet.